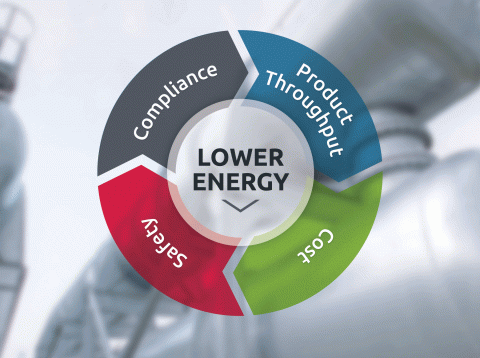
As applications for new and innovative products are continually expanding, manufacturing is faced with added environmental regulations, as well as compressed margins to meet demand. Thus, plants must constantly drive to improve their competitiveness by streamlining their operations and reducing costs wherever possible. When industrial processes are designed with Energy Savings in mind, production, safety and cost efficiencies are all increased to create higher profits and better competitive positioning.
Here are five (5) things to consider in order to achieve greater profitability:
- Focus on the Large Energy Costs: Use the 80/20 rule; 80% of energy is consumed by 20% of the processes. What is the most costly operation in your manufacturing process? How much energy is consumed? How can that energy be minimized?
- Review Process Heating Equipment: The higher the operating temperature, the more costly the fuel/energy will be. What advanced combustion equipment do you use? At what temperatures do they operate? What fuel is used? How can this be optimized?
- Investigate the use of flexible Gases & Solvents: Using gases and solvents is necessary in many Industrial Processes. What are the cost implications of burning solvents, SYNGAS and other combustibles vs. traditional fuels? What are the safety impacts to plant?
- Know your Environmental Regulations: In many cases, the VOC abatement control technology is the limiting factor in manufacturing operations. Can the VOCs be reduced, reused, or recycled? What opportunities can you achieve if your VOC Abatement equipment is optimized or minimized?
- Measure and Control: “If you can’t measure something, you can’t understand it. If you can’t understand it, you can’t control it. If you can’t control it, you can’t improve it.” – H. James Harrington
Would you like to learn more?
Join us for our Savings, Safety & Sustainability Webinar Sept 11 @ 10am EDT
Add new comment