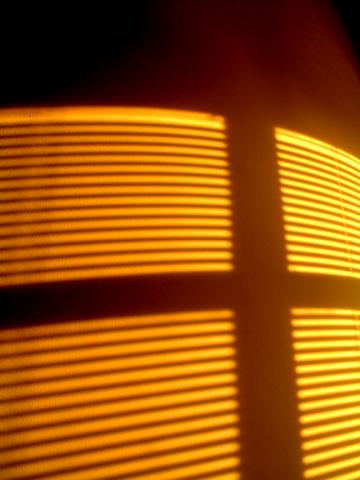
Because the analyzer response time is critical, large pre-conditioning filters in the sample line are to be avoided. The delay in a filter can be estimated by dividing the filter volume by the sample flow rate through the filter.
The loading, or accumulation of particulates and contaminates in the filter, is proportional to the amount of particulates in the sample stream and the flow rate through the filter. In cases where a high amount of particulates are found in the sample stream, commonly a larger filter is used to increase the maintenance interval on the filter. However, a larger filter results in a significant time delay in transport of the sample to the analyzer.
Efforts to eliminate this added delay through increasing the sample flow rate of the analyzer, or by the addition of a bypass flow loop in the sample line, will increase the amount of sample flow and particulates the filter must handle, and cause the loading of the filter to increase to a point where it negates the extra filter capacity. Only through the application of a filter with a very high surface area and low volume, such as an in-line sintered metal filter, can an advantage in filtering be obtained without a large delay in analyzer response time.
Preconditioning systems that use refrigerated chillers to remove water vapor and condensables are unacceptable. Even where the flash point of the solvent is very low, the condensate can remove water soluble solvents. Filters or other components in the sample system which accumulate any liquid whatsoever indicate insufficient heating of the sampling system and the potential for false low readings.
Add new comment