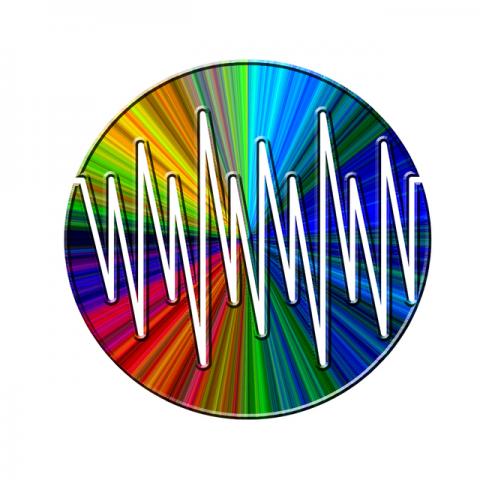
Last week we discussed the first type of process upset that could present a hazardous condition, the steady-state, this week let's focus on on the condition that poses the greatest difficulties in detection and correction.
Process upsets from transient conditions produce a hazard from an unstable process that is changing relatively quickly. Causes include:
- excessive acceleration of line speed
- loss of control of solvent metering
- loss of ventilation
- loss of web tension
Experience has shown that these sudden changes can produce the most hazardous conditions, and at the same time the most difficult challenge for detection and correction. Among the more serious accidents, it is not uncommon for an explosion to have occurred within a few seconds of an uncontrolled increase in solvent load.
Transient conditions are corrected only by a fast, accurate analyzer system that can produce an alarm in time for effective corrective action. Critical factors include:
- Dryer volume versus ventilation rate
- Rate of solvent increase
- Initial accuracy of the analyzer
- Analyzer calibration
- Analyzer response time
- Normal operating level
- Alarm level(s)
- Type of corrective action(s)
- Speed of corrective action(s)
Sudden changes greatly reduce the margin of safety. Even an analyzer that has good accuracy can have a tremendous “dynamic error” due to delays in making a reading. Seen in this light, many existing analyzer systems are inadequate.
In years past, various authorities had recognized that an analyzer provides a significant safety improvement only if it “continuously” measures the solvent concentration. More recently, they have begun to indicate the need for prompt response times on the order of a few seconds. This calls for analysis of the potential upsets, analyzer response and corrective action to determine if the analyzer response is fast enough. At the start, it is already clear that response times must be faster than those required under industry standards for general-purpose combustible gas detectors. This indicates the need for a class of analyzer designed specifically for use in solvent vapor monitoring applications.
Add new comment