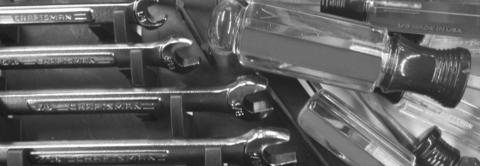
Coil coating line managers report that they experience three basic problems in solvent vapor monitoring, this week let’s address the first one:
- Maintenance is burdensome. Sample lines clog, pumps break down, and analyzer elements become fouled - all resulting in excessive labor and costly downtime.
Coil coating ovens typically operate at high temperatures, with some zones at over 800°F. This temperature range is needed to cure organic polymer coatings to their substrate materials.
Solvents are typically vaporized in the early oven zones. At the same time, however, other materials are also vaporized: resins, plasticizers, additives, and other compounds.
Most monitoring problems arise because these materials condense when the sample temperature drops and becomes too low to maintain a vapor state. In very little time, the sample lines, analyzer, and sample pump can become fouled and clogged, causing frequent downtime to dismantle and clean the system.
So what’s the solution?
A solvent vapor monitoring system that operates at a high temperature, has no external samples lines or moving parts, and offers intelligent predictive maintenance alerts.
Our PrevEx® Flammability Analyzers do just that:
- Excellent in High Temperature Processes - The PrevEx’s operating temperature is high enough to keep all oven atmosphere elements in the vapor state. It’s materials of construction allow sampling in oven atmospheres above 800°F. These very high oven and sample temperatures in no way impede the analyzer’s operation.
- Simple Flow System Prevents Maintenance Issues - The analyzer further avoids condensation and maintenance problems through its simple flow system, which has no capillaries that can clog or pumps that can fail. It also mounts directly on the oven wall or exhaust duct without external sample lines.
- Efficient Operation Reduces Maintenance - The PrevEx is a complete stand-alone LFL system, that’s easily operated and maintained. It features predictive maintenance, a “service needed” message and relay contact, which anticipates the need for maintenance before faults occur. Its efficient operation, like the avoidance of sample condensation, reduces service to routine maintenance.
Add new comment