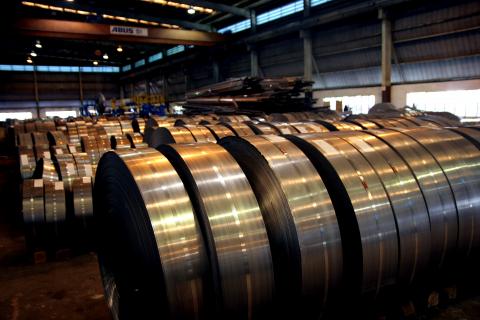
Coil Coating is a complicated process, in fact it is the most advanced method for coating metal.
According to the National Coil Coating Association "it is a continuous, automated process for coating metal before fabrication into end products. The steel or aluminum substrate is delivered in coil form from the rolling mills. The metal coil is positioned at the beginning of the coating line, and in one continuous process, the coil is unwound, pre-cleaned, pre-treated, pre-primed, and pre-painted before being recoiled on the other end and packaged for shipment." And all of this happens at up to 700 feet per minute!
The following steps take place on a modern coating line:
- Stitching the strip to the previous coil
- Cleaning the strip
- Power brushing
- Pre-treating with chemicals
- Drying the strip
- Applying primer on one or both sides
- Curing (often only 15 to 60 seconds!)
- Cooling the strip
- Top coating on one or both sides
- Second curing
- Cooling down to room temperature
- Rewinding of the coated coil
That's a lot of complex steps going on in one process...but being safe shouldn’t have to be one of them.
Imagine if something goes wrong, like say a fire or explosion, during one of these steps, how complicated is that going to be to resolve?
One of our customers (before they purchased our equipment) had a fire on their coil coating production line that led to:
- Temporary shut down, stop of production
- Purchase of a brand new coil coating line, due to extensive damage
- Asking a competitor to produce their product during the downtime
You know what would have been simple? Installing a safety system beforehand.
Safety and fire codes outline the design specifications for the safe operation of solvent ovens. The codes limit the maximum solvent concentration allowable to 25% of the LFL under worst case operation. Large volumes of ventilation air must be heated and circulated to keep the solvent vapors in the oven at safe operating levels.
However, if a flammable vapor analyzer is installed (which is just what they did!) as a safety control the maximum allowable concentration is 50% of the LFL, which means not as much air has to be heated to dilute the vapors.
So you can operate safely and save on fuel... sounds like a really simple solution.
Add new comment