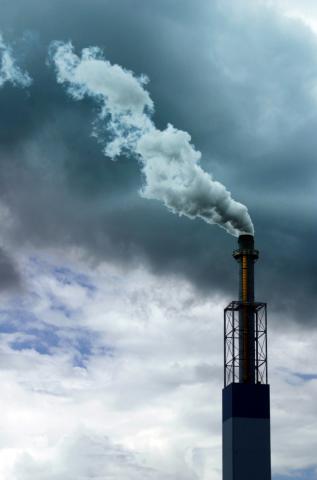
For the past couple weeks we shined the spotlight on the Pollution Control Industry; we've looked at the three ways to reduce emissions (Oxidizers, Incineration & Solvent Recovery). This week let's discuss HOW, by looking at real life applications:
Incineration Case History
A worldwide manufacturer for the adhesive labeling and semiconductor markets, uses different solvents that are evaporated off in a heating process, collected and then directed to an incinerator for destruction. They wanted to monitor the flammability of the process exhaust stream going into its incinerator to avoid danger or an explosion if the inlet stream to the incinerator suddenly gets rich enough to ignite. They needed an analyzer that could measure their wide range of chemicals, as well as highly corrosive compounds, preferably a Hastelloy constructed analyzer to handle the harsh environment. The Company chose Control Instruments’ PrevEx Model SNR674 analyzers after a three year investigation of all the technologies available.
- The PrevEx is constructed of hard-coat aluminum and well suited for their application. It is fully heated to keep the sample stream in vapor form eliminating potential corrosion and the need for Hastelloy construction. It has the unique ability to accurately measure the total flammability of all the constituents in the process exhaust stream.
Find out more details.
Waste Wood Case History
- The CalorVal completely burns the sample and therefore is a direct measure of Total Calorific Value. It is fully heated to 120°C to prevent condensation and minimize downtime due to clogging. It provides an accurate and continuous measurement of the BTU content in real time mode.
Find out more details.
Solvent Recovery Case History
A global manufacturer uses a Solvent Recovery System to recover and re-use solvents from its manufacturing process. Two carbon beds are used, so that one bed can process the solvent-laden air while the other one is regenerating, a timer is employed to make the switches between them. They felt the timer might be switching the beds too early or too late especially as the carbon beds began to age and become less adsorbent. Early switching means the process is operating at less than total efficiency and late switching results in breakthrough to the atmosphere resulting in penalties and fines. They wanted to accurately measure the saturation of the carbon beds and control the switching between beds in real-time.
- They chose the SNR650 Flame Ionization Detector to do this job. Its industrial design monitors the hydrocarbon levels in real-time and reacts quickly to switch beds. Each steam-down cycle recovers the maximum amount of solvent, lengthening the life of the carbon-bed itself and there are no accidental solvent emissions released from the bed.
Find out more details.
Add new comment