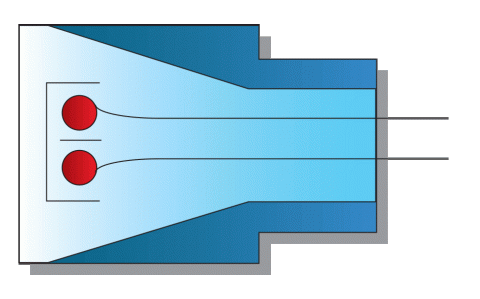
Catalytic-bead sensors are constructed of two small wire coils covered with a catalyst. One coil is “active” while the other is rendered inert and acts as a reference. A flow of electrical current through the internal coils heats the catalytic coating to a temperature at which the active coil will react with many flammable vapors and gases. This reaction occurs in the form of surface combustion which in turn causes an increase in the sensor’s temperature. The resulting temperature change is converted into an LFL reading.
The intensity of the catalytic reaction varies for different flammable substances. Therefore, response factors vary considerably, resulting in potentially inaccurate readings. Calibration correction may be required for each different solvent or solvent mixture used in the process.
- Catalytic sensors have slow response times, as much as 15 seconds is not unusual. That slow response alone may eliminate a catalytic sensor from consideration as a process monitoring device.
- Catalytic sensors are not failsafe. During operation they cannot detect and alarm all conditions that can cause the sensor to become non-functional. There are fault conditions that can only be detected by performing a calibration. This can lead to a false sense of safety, as it has no means of warning the operator that it is not functioning properly.
Because of these characteristics, catalytic sensors are typically used only as leak detectors. They are generally well suited to area-monitoring applications where response times of ten or more seconds are acceptable; where the atmosphere does not contain condensate, dirt or dust; is not heated and is normally free of flammable vapors.
Add new comment