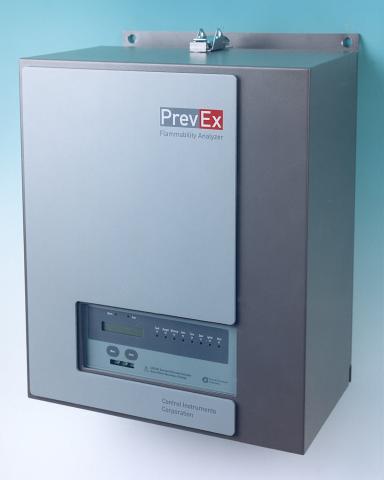
For the past couple weeks we shined the spotlight on the Solvent Based Printing application; WHAT goes on and WHICH hazards they face. This week let's discuss HOW you can save on costs through monitoring, by looking at real life applications:
Solvent Based Printing 101 Case History
A state of the art printing press, which consists of several stations with at least one dryer so that solvents can be evaporated off, uses large amounts of heated air to ventilate & keep solvent vapor concentrations below 25% of the LFL, as directed by the NFPA safety code. The Company was looking to reduce these heated air costs without affecting their production rates or violating the safety directives.
After some investigation and education on the applicable NFPA codes, they found that codes allow a substantial reduction in air in cases where a continuous solvent vapor analyzer is installed. They chose to install PrevEx Flammability Analyzers due to their unique ability to:
- accurately measure the total flammability of all the constituents in the process
- are not susceptible to coating or poisoning by resins or other plasticizers or silicones
- keep all the elements in the dryer atmosphere in the vapor state eliminating clogging and sample condensation
A manufacturer and supplier of coated and laminated films & adhesive products was looking to reduce ventilation air and fuel costs without affecting production rates or violating the NFPA safety directives. They were using large amounts of heated air to ventilate the dryers to keep the solvent vapor concentration below 25% LFL as directed by the NPFA codes.
However, the codes allow a substantial reduction in air in cases where a continuous solvent vapor analyzer is installed. When such instruments are installed to continuously sample the exhaust of a dryer zone, the vapor concentration in that zone is allowed to rise as high as 50% LFL.
The company chose to install PrevEx Flammability Analyzers on their dryers so they could run above 25%LFL. This allowed them to reduce costs while maintaining safety and production levels.
They chose the PrevEx because they change their ink mix regularly and they did not want to have to recalibrate each time they did. With the “Universal Calibration” capability of the PrevEx, they don’t have to recalibrate when these changes occur. This allows them to continue production and avoid downtime associated with re-calibration. The PrevEx gives consistent and reliable readings with multiple or changing solvent concentrations.
Find out more details.
Gravure Printing on Film Case History
A product labeling manufacturer products was using PrevEx Flammability Analyzers on one of their print lines and infrared detectors on another to continuously monitor the % LFL of the varying solvent levels in the dryers in order to maintain safety. However, they were experiencing inconsistent readings with the infrared detectors, leading to a loss of confidence in the detection method.
The Company made the decision to remove the IR detectors and replace them with PrevEx Flammability Analyzers, similar to the ones they had on print line one. The analyzers give consistent and reliable readings. Unlike the infrared detectors, they accurately measure mixtures of solvents and are not susceptible to fouling, coating or poisoning by resins or any other plasticizer or silicones. The analyzers feature fast response, failsafe operation, low maintenance and easy servicing.
- After some time the Company went through an expansion and needed to add two lines to its process. They worked with their OEM exclusively for a turnkey solution—installation, start-up and maintenance. The new lines were equipped with PrevEx Flammability Analyzers.
Add new comment