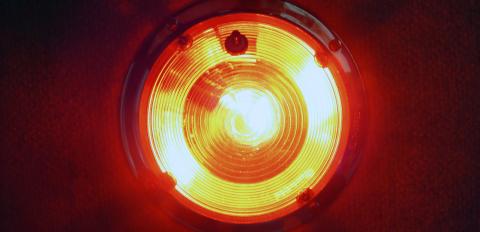
The conversation around Safety Integrity Level (SIL) has picked up among the industrial community; but what exactly is everyone saying and how does it apply to YOUR process?
Let’s attempt to break down this often-misunderstood concept and learn how it can be implemented properly. To fully understand a complex concept like SIL, there are a few other aspects to consider, last week we looked at functional safety, this week let's focus on Safety Instrumented Systems (SIS).
Safety Instrumented System (SIS)
According to the American Institute of Chemical Engineers, a safety instrumented system (SIS) "takes automated action to keep a plant in a safe state, or to put it into a safe state, when abnormal conditions are present. It may implement a single function or multiple functions to protect against various process hazards in your plant".
The SIS plays a crucial role, providing a protective layer for industrial process systems that can prevent hazardous conditions or mitigate their effect. Its purpose is to take a process to a “safe state” when pre-determined controls are surpassed or when safe operating conditions have lapsed.
The SIS is comprised of Safety Instrumented Functions with:
- sensors (for signal input & power)
- logic solvers (for power & communications)
- actuators (for final control)
An SIS is made up of several Safety Instrumented Functions (SIF), usually with different safety integrity levels (SIL), which is why it shouldn't be described by a single SIL.
Add new comment